Digital Temperature Control Systems
We are excited to be working with Watttron, bringing their thermoforming and sealing technologies to Australia.
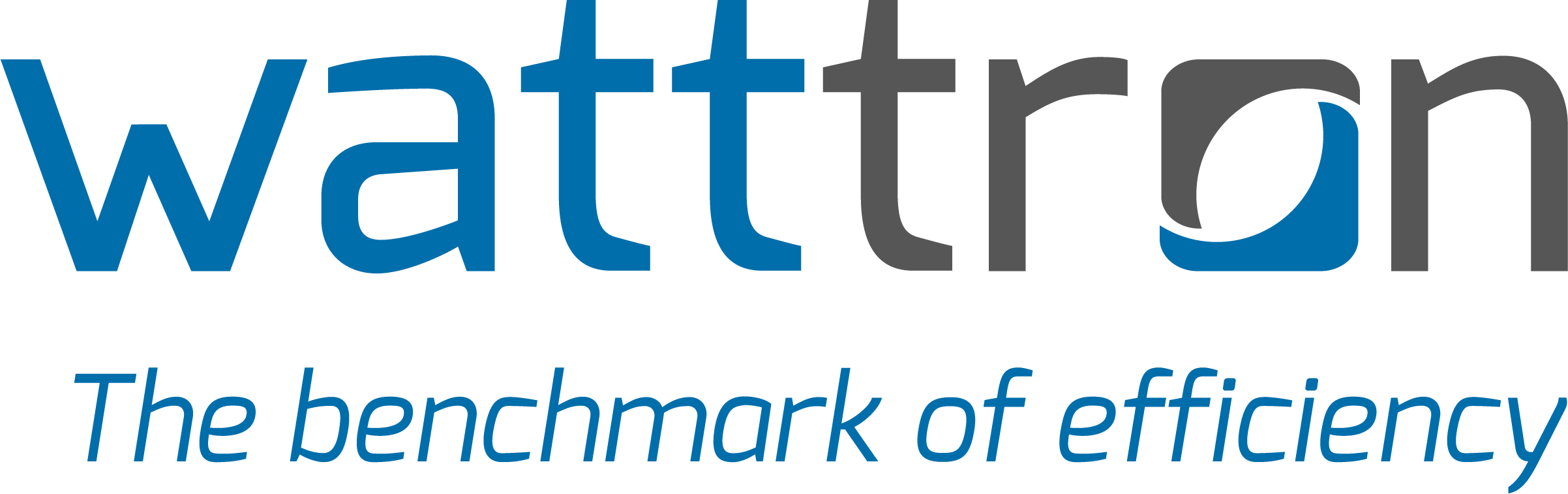
Why consider digital heating/sealing technologies in your packaging process?
- You can save energy since the heat is supplied directly to the point of use.
- Temperature control is amazingly precise. Temperature is controlable to 1°C and has fully adjustable heat mapping down to 6mm X 6mm resolution (pixel).
- Instant feedback and control. Each heat pixel has its own temperature sensor and each individual pixel can be controlled. As heat is drawn off, more is supplied within milliseconds.
- Save time, startup and shutdown is seconds rather than minutes.
When used with plastic thermal forming, you can start with thinner roll stock material, control the stretch and have better quality tubs and forms. Corners are programmed to be as thick as the base and walls.
For plastic bag, pillow and pot sealing, and thermal forming, you can retro fit this to existing machines.
This is a great innovation enabling a major step towards sustainable and circular packaging.
Watttron in the News
- APPEX Video: watttron’s Marcus Stein & Tobias Honig – PKN Packaging News
- Watttron raises €12m to advance sustainable packaging solutions – Packaging Gateway
- Mespack and Watttron integrate smart digital sealing technology into flexible packaging machinery – Packaging Europe
- Volpak and Watttron implement digital sealing into horizontal pouching machinery – Packaging Europe
- New Tech Comes to Heat Seal Bars – Packaging World
Watttron Cera2heat – Thermoforming for tubs/cups
Watttrons patented cera2heat® matrix heating system enables heterogeneous, precisely defined contact heating of surfaces for thermoforming packaging for food and beverage applications.
The system is designed around a large number of regularly arranged, small heating pixels. The temperature of each pixel can be individually programmed and controlled – this gives incredible precision to the process.
The heating system consists of 40 x 40 mm modules. These can be arranged in any order and combined to form individual areas. Thanks to its modular design, cera2heat® can be installed or retrofitted in almost any machine.
- Heating rates: up to 100 K/s
- Temperature range: up to 200°C (higher temperatures on request)
- Power range: up to 50 W/cm²
- Production ready within a few seconds
- Realizable heating area: practically unlimited due to modular concept
- Size of a heating pixel: 5 mm × 5 mm
- Size of one module: 40 mm × 40 mm (8×8 heating pixels)
- Integrated temperature sensors on heating surface for optimal process control and temperature control accuracy
- Control hardware integrated, operation via user interface (GUI) or by integration into machine control system
Watttron Cera2seal – Sealing/welding for lids/membranes
The Watttron cera2seal® heating system is specially designed for plastic sealing and welding processes, such as plastic membranes over plastic cups/tubs.
Temperature sensors are integrated on the surface for precise control of the actual temperature distribution. This allows the sealing of plastics that have traditionally been difficult to work with – such as the more recycling-friendly Polypropylene.
- Heating rates: up to 50 K/s
- Sealing temperature range: up to 200°C (higher temperatures on request)
- Power range: up to 200 W/cm²
- Production ready within a few seconds
- Realizable heating area: application specific
- Close proximity of heating circuits and temperature sensors to the sealing surface for optimum process control and temperature control accuracy
- Control and regulation hardware integrated or as control cabinet temperature controller, integration into machine control system by means of common fieldbus protocols (EtherCAT, Ethernet/IP etc.)
- Heating and sensor circuits in close proximity to the sealing surface for optimal optimum process control and temperature control accuracy
- Control and regulation hardware integrated or as control cabinet temperature controller
- Integration into machine control system via common fieldbus protocols (Modbus/TCP, Ethernet/IP etc.)
Need A Quote Or Have Questions?
We'll take a look and come back to you ASAP.